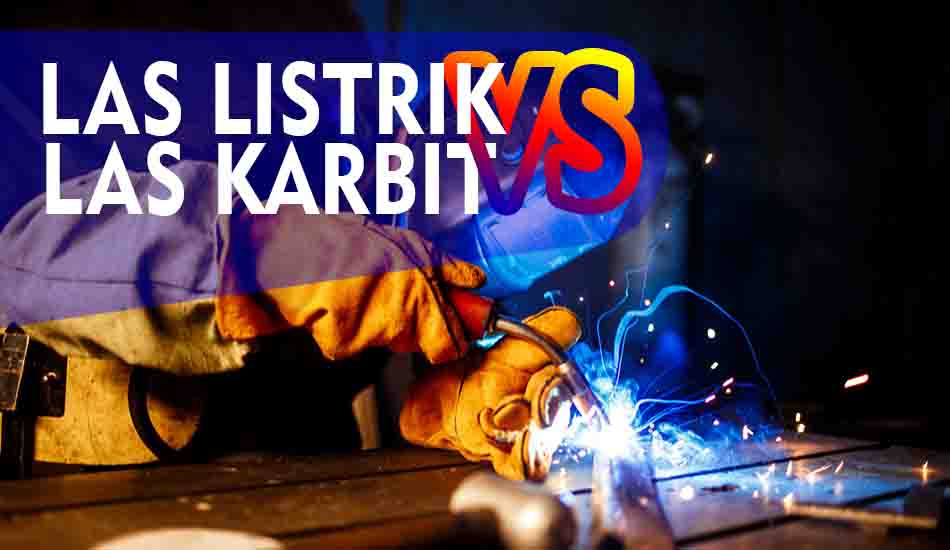
Perbedaan Las Listrik vs Las Karbit
Pada kesempatan kali ini, kita akan mencoba membahas tentang perbedaan Las Listrik dan Las Karbit, mana yang efisien.
Dua metode yang paling umum digunakan yaitu las listrik dan las karbit. Meskipun keduanya bertujuan untuk menyatukan logam, proses dan aplikasi idealnya sangat berbeda.
Memahami perbedaan mendasar kedua ini sangat krusial, baik Anda seorang pelajar yang baru memulai perjalanan di dunia teknik pengelasan atau seorang teknisi berpengalaman yang mencari solusi yang lebih efisien.
Bahkan seorang penggemar DIY yang ingin mencoba coba proyek logam di bengkel rumahan.
Pilihan antara las listrik dan las karbit tidak hanya mempengaruhi hasil akhir pekerjaan, tetapi juga faktor keselamatan, biaya dan efisiensi waktu.
Pengetahuan yang tepat akan membantu Anda membuat keputusan yang paling tepat untuk setiap proyek pengelasan yang dihadapi.
Semoga uraian berikut ini memberikan pemahaman yang komprehensif dan membantu Anda menentukan metode pengelasan yang ideal.
Baca juga : Perbedaan Kawat Las LB 52 dan LB 52 U
1. Sumber Energi dan Proses Pengelasan
Perbedaan paling fundamental antara las listrik dan las karbit terletak pada sumber energi yang digunakan untuk menghasilkan panas yang dibutuhkan untuk melelehkan logam.
Pada Las listrik, sebagaimana namanya memanfaatkan energi listrik untuk menciptakan busur listrik.
Busur listrik ini yang dihasilkan antara elektroda dan bahan kerja, menghasilkan panas intens yang cukup untuk mencairkan logam dan menciptakan sambungan yang kuat.
Jenis arus listrik dan jenis elektroda yang digunakan (SMAW, MIG, TIG) mempengaruhi karakteristik lasan, seperti penetrasi dan kerapian.
Proses ini sering kali lebih efisien untuk pekerjaan skala besar dan logam yang lebih tebal, sesuai dengan kebutuhan industri manufaktur dan konstruksi berat.
Di sisi lain, las karbit memanfaatkan reaksi eksotermik pembakaran campuran gas asetilena (dari karbit) dan oksigen untuk menghasilkan nyala api yang sangat panas.
Nyala api ini yang diatur dengan presisi oleh tukang las, mencairkan logam induk.
Menghasilkan sambungan yang lebih halus dan rapi. Teknik ini lebih cocok untuk pekerjaan detail dan logam yang lebih tipis.
Perbedaan sumber energi ini juga berdampak pada portabilitas peralatan dan biaya operasional yang akan kita bahas lebih lanjut.
Serta pelatihan dan keahlian yang mumpuni juga sangat diperlukan untuk memaksimalkan kemampuan dan keselamatan kerja.
2. Jenis Logam dan Ketebalan yang Cocok
Kemampuan dalam menangani berbagai jenis dan ketebalan logam menjadi perbedaan yang signifikan.
Las listrik, berkat variasi jenis elektroda dan teknik pengelasan (SMAW, MIG, TIG).
Memiliki fleksibilitas yang lebih tinggi dalam menangani berbagai material logam. Mulai dari baja karbon, baja tahan karat, hingga aluminium.
Kemampuannya untuk mencairkan logam dengan ketebalan yang lebih signifikan (lebih dari 2 mm), menjadikannya pilihan utama dalam industri konstruksi dan manufaktur berat.
Mesin las listrik modern, khususnya jenis inverter, semakin ringkas dan portabel, sehingga cocok untuk berbagai aplikasi, termasuk di lokasi pekerjaan lapangan.
Sebaliknya, las karbit secara tradisional terbatas pada logam dengan ketebalan yang relatif tipis (kurang dari 2 mm) dan sering digunakan untuk pekerjaan detail atau reparasi.
Meskipun dapat digunakan pada beberapa jenis logam seperti besi dan aluminium, tingkat kesulitan dan hasil yang memuaskan akan sangat ditentukan oleh ketebalan bahan dan keterampilan tukang las.
Pilihan jenis logam dan ketebalan yang sesuai menjadi unsur penting dalam perencanaan dan eksekusi proyek pengelasan.
3. Biaya Operasional dan Efisiensi
Perbedaan biaya operasional antara kedua metode ini perlu dipertimbangkan.
Pada Las listrik, meskipun membutuhkan investasi awal untuk mesin las, cenderung lebih ekonomis dalam jangka panjang, khususnya untuk proyek dengan volume pekerjaan besar.
Biaya utama adalah listrik yang dikonsumsi dan elektroda yang terpakai yang relatif terjangkau.
Efisiensi las listrik khususnya MIG dan TIG tergolong tinggi, mampu menyelesaikan pekerjaan dengan lebih cepat.
Las karbit, di sisi lain, memiliki biaya awal yang relatif lebih rendah karena peralatannya yang lebih sederhana. Peralatan utama adalah obor las dan tabung gas asetilena.
Namun, biaya operasional jangka panjang cenderung lebih tinggi karena harga gas asetilena yang lebih mahal dan kebutuhan penggantian tabung gas secara berkala.
Efisiensi las karbit dipengaruhi oleh kecepatan pengerjaan tukang las dan kompleksitas proyek.
Perlu dipertimbangkan bahwa jenis las karbit ini lebih cocok pada pekerjaan pekerjaan yang memerlukan ketepatan, kerapian dan detail yang tinggi.
Oleh karena itu, pemilihan metode perlu mempertimbangkan aspek ekonomi dan skala proyek.
Baca juga : Perbedaan Hollow dan Baja Ringan, efisien yang mana
4. Tingkat Keselamatan dan Risiko
Baik las listrik maupun las karbit memiliki potensi bahaya yang perlu diwaspadai dan diantisipasi.
Las listrik membawa risiko sengatan listrik, terutama jika dilakukan tanpa pelatihan yang memadai dan tanpa penerapan standar keselamatan kerja yang tepat.
Penggunaan APD, seperti sepatu las isolasi dan sarung tangan yang sesuai, sangat penting.
Selain itu, busur listrik yang dihasilkan dapat menyebabkan kerusakan mata jika tidak dilindungi dengan kacamata las.
Sementara itu, las karbit membawa risiko yang berbeda, yaitu potensi ledakan atau kebakaran jika tidak ditangani dengan hati hati.
Gas asetilena yang mudah terbakar membutuhkan penanganan dan penyimpanan yang aman serta penggunaan peralatan yang dalam kondisi baik.
Baik las listrik maupun las karbit menghasilkan percikan api dan panas yang ekstrem, sehingga penggunaan APD seperti baju las dan masker las menjadi sangat penting untuk melindungi kulit dan saluran pernapasan.
Penggunaan APD dan pelatihan yang baik akan meminimalkan risiko kecelakaan pada kedua metode pengelasan.
Pelatihan khusus penting untuk memahami prosedur keselamatan bagi masing masing teknik pengelasan.
Kesimpulan
Meskipun keduanya merupakan metode pengelasan yang umum, las listrik dan las karbit memiliki perbedaan signifikan dalam hal sumber energy.
Jenis dan ketebalan logam yang dapat dilas, biaya operasional dan risiko keselamatan.
Pemilihan metode yang tepat bergantung pada kebutuhan spesifik proyek, keterampilan operator serta pertimbangan biaya dan keselamatan.
Dengan pemahaman yang mendalam tentang perbedaan perbedaan ini, diharapkan Anda dapat membuat keputusan yang tepat dan aman dalam setiap proyek pengelasan.